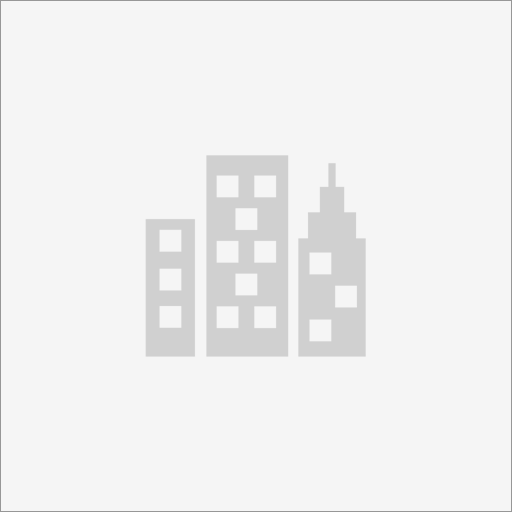
Website American Plastic Molding
Why American Plastic Molding?
Amercian Plastic Molding gives an opportunity to work at an employee-owned plastic manufacturer where you are part of a company that values collaboration, accountability, and long-term success. The employee ownership structure fosters a sense of pride and responsibility. Additionally, the plastic manufacturing industry presents unique challenges and opportunities to innovate and allows you the ability to have a sustainable impact to the business.
Key Responsibilities:
- Quality Control & Assurance:
- Develop, implement, and maintain quality standards, policies, and procedures in accordance with ISO 9001 and ISO 14001 standards or other relevant standards.
- Conduct regular inspections and tests on molded products to ensure compliance with customer specifications and regulatory requirements.
- Oversee the documentation and analysis of quality data (e.g., defect rates, non-conformance reports, corrective actions).
- Ensure that all incoming raw materials meet the necessary quality standards before they are used in production.
- Monitor and report on key performance indicators (KPIs) related to quality and compliance such as defects and corrective action requests.
- Manage the timely completion of APQP documentation such as flow diagrams, PFMEA, Control Plans, Gauge R&R, PSW, capability studies, and measurement system analysis.
- Manage the development and implementation of quality documentation, such as procedures, policies, and work instructions.
- Work with customers on PPAP and Engineering Change approvals and deviations.
- Team Leadership & Training:
- Lead and mentor quality technicians and other quality staff within the department.
- Conduct training sessions for employees on quality standards, best practices, and safety protocols.
- Foster a culture of quality across all teams, ensuring everyone is committed to maintaining high standards.
- Process Improvement:
- Analyze production processes and identify areas for improvement to reduce defects and increase efficiency.
- Work closely with engineering and production teams to troubleshoot issues and implement corrective actions.
- Lead initiatives for continuous improvement (e.g., Six Sigma, Lean Manufacturing) to enhance product quality and production efficiency.
- Conduct root cause analysis and implement corrective and preventive actions (CAPAs) for quality and compliance issues.
- Compliance & Audits:
- Ensure compliance and able to get through an audit with industry-specific regulations and standards (e.g., ISO 9001, ISO 14001, BIFMA, LIL, MIL and ASTM).
- Lead internal and external audits, ensuring all practices adhere to regulatory and company standards.
- Manage the preparation of reports for audits, certifications, and inspections.
- Customer Interaction:
- Work with customers to address quality-related concerns and ensure that customer specifications are met.
- Provide feedback and insights to the product design and engineering teams to help prevent future quality issues.
- Analyze customer complaints and returns, identifying root causes and implementing corrective actions.
- Conduct supplier audits and assessments to ensure compliance with quality and environmental requirements.
- Collaborate with suppliers to resolve quality and environmental issues and improve supplier performance.
- Reporting & Documentation:
- Prepare and present quality performance reports to upper management, highlighting trends, risks, and opportunities for improvement.
- Maintain thorough documentation of quality activities, inspections, audits, and corrective actions taken.
MINIMUM QUALIFICATIONS (Knowledge, Skills, and Abilities)
- Bachelor’s degree in quality management, or a related field.
- In-depth knowledge of quality management systems (QMS) and regulatory requirements (e.g., ISO 9001, ISO 14001, IATF, BIFMA, UL regulations).
- Certifications in Quality Management (e.g., Six Sigma, ISO 9001) are a plus.
- At least 5-7 years of experience in a quality management role within a manufacturing environment, preferably in the molding or plastics industry.
- Experience with molding processes such as injection molding, blow molding, or compression molding is highly desired.
- Strong knowledge of quality control methodologies and industry standards.
- Excellent problem-solving, analytical, and organizational skills.
- Familiarity with statistical process control (SPC), root cause analysis, and quality management software tools.
- Strong communication and leadership skills.
- Ability to manage multiple priorities in a fast-paced production environment.
- Detail-oriented and able to maintain high standards under pressure.
- Willingness to collaborate with different teams to drive quality improvement initiatives.
PHYSICAL DEMANDS:
The physical demands outlined below are essential for successfully performing the duties associated with this position. Reasonable accommodations will be considered for individuals with disabilities.
While performing the job, the employee is required to talk or listen. The employee will frequently stand, sit, and walk, and will manipulate objects with hands and fingers. Additionally, the employee may be required to reach with hands and arms, climb or balance, and stoop, kneel, crouch, or crawl. The employee must frequently lift and/or move up to twenty-five pounds and occasionally lift and/or move up to fifty pounds. Specific vision abilities required by this job include close vision, distance vision, and the ability to adjust focus.
WORK ENVIRONMENT:
Occasionally, the employee may be exposed to moving mechanical parts, airborne particles, and hot liquids. The noise level in the work environment is usually moderate.
CORE VALUES:
- Operate With Transparency
- Make A Difference Everyday
- Fix It For Good
- Play For Each Other
- Thankful
NOTE: The first responsibility of each APM employee is customer satisfaction. Each employee of APM will support the quality and the environmental systems.
This job description in no way states or implies that these are the only duties to be performed by the employee(s) in this position. Employees will be required to follow any other job-related instructions and to perform any other job-related duties requested by any person authorized to give instructions or assignments. All duties and responsibilities are subject to possible modification to reasonably accommodate individuals with disabilities. To perform this job successfully, the incumbents will possess the skills, aptitudes, and abilities to perform each duty proficiently. Some requirements may exclude individuals who pose a direct threat or significant risk to the health or safety of themselves or others. The requirements listed in this document are the minimum levels of knowledge, skills, or abilities. This document does not create an employment contract, implied or otherwise, other than an “at-will” relationship.
The company is an Equal Opportunity Employer, drug-free workplace, and complies with ADA regulations as applicable.
APM reserves the right to make hiring/promotional decisions outside of these qualifications and reserves the right to waiver qualifications.
To apply for this job please visit secure6.saashr.com.